Quality
Quality ASSURANCE
Pharmaceutical Industries - High-Purity Gases & Systems - Ultra-high purity semiconductor fabs
Umech operate an extensive Quality Management System based on ISO:9001 with a focus on;
Continuous improvement - Customer satisfaction - Operational consistency
Let us develop customised Quality & Project Plans (QPP’s) or Inspection and tests plans (ITP’s) appropriate for your project. Our capabilities include Pharmaceutical industry level cGMP/GDP validation programs including IQ/OQ/PQ .
Pressure Testing
Standard purity and Ultra High Purity (UHP) pressure testing.
Gas system stress testing for high pressure filling and mixing applications.
Line tracing using fluid continuity checks.
Leak testing using high accuracy digital pressure monitoring instruments.
Helium Leak Detection
Utilising mobile, state of the art equipment to achieve leak rates of up to1x10-11mbar/l/s for standard stainless steel and UHP gas systems. Weld integrity testing for hazardous, high purity gas delivery systems. Highest accuracy leak detection available on the market, quickly find the smallest leaks while maintaining system purity. Outboard (sniffer) helium leak testing is also available.
Moisture Testing
Oxygenated contaminants such as water vapor in materials used and in the wafer environment are primary causes of defects and process variations that compromise yield.
Cavity Ring-Down Spectrometer (CRDS) can perform H2O analysis over a vast range: 12 ppb to 2000 ppm in N2!
Calibration/Verification of Dew Point sensors
Confirmation of line moisture contribution
Verification of recovery of system purity
Particle Count Testing
Our team are experts in testing particle contamination to 0.3 - 10 𝜇um. Our test unit is designed to be integrated into your environmental monitoring program.
A totally sealed pharmaceutical grade Polycarbonate blend enclosure and is fully VHP compatible
Fully compliant to 21CFR part 11
Built-in cleanroom certification reports
NATA certified calibration
Derouging & Passivation
Umech’s custom built passivation skid can remove internal surface contamination from your piping system.
Nitric or Citric acid process
Safe, efficient and controlled passivation and flushing process for your facility
Pharmaceutical plants, vaccine manufacturing WFI and purified water systems.
Less risk of contamination-related production losses and unplanned system shutdowns
Commissioning & Validation
Our validation methodology is based around the Validation V-model and can be customised to suit various industries.
User Requirements Specification
Functional Specification
Technical specification
Design Qualification
Installation Qualification
Operation Qualification
Performance Qualification



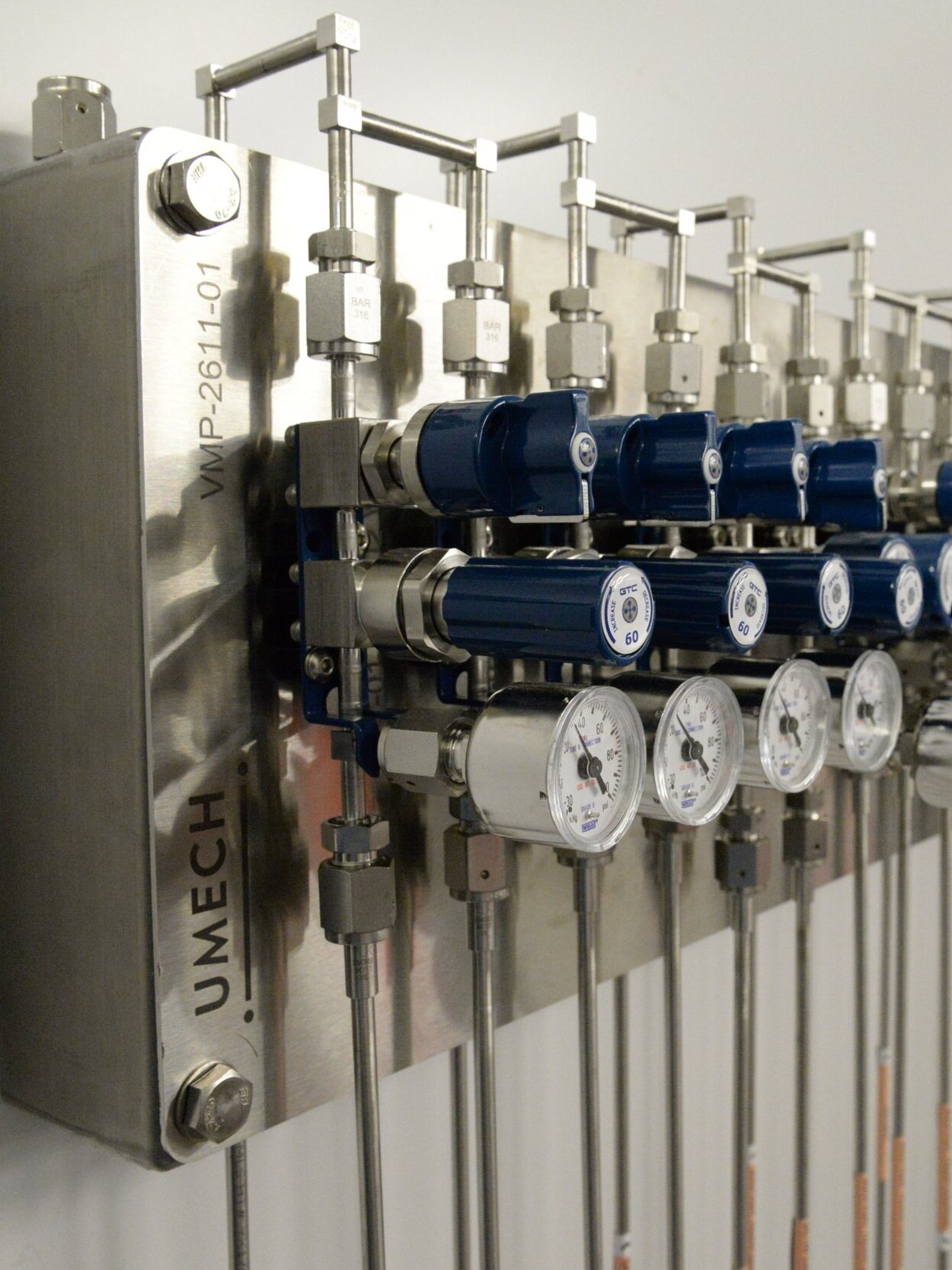


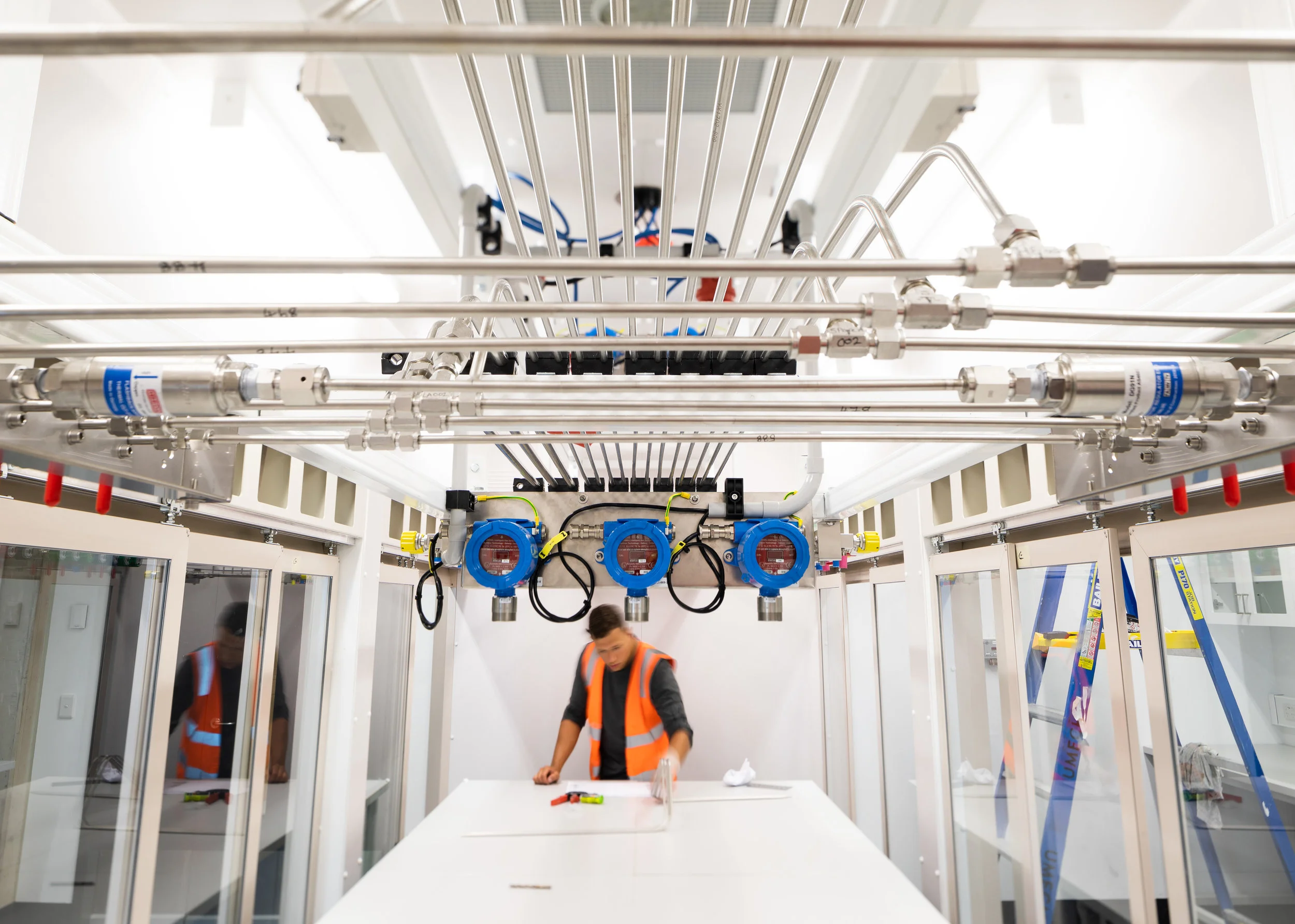

